Manufacturing Optimization – The Paradigm Shift to A Smarter System
There is no sitting on the fence with manufacturing transformation in a post Covid-19 world, the value of smart manufacturing takes on an added dimension. In this unexampled signal of the pandemic most of the organizations have struggled for a faster response to the disruptive challenges and restoring their operations. Research indicates that most of the sectors witnessed unparalleled changes during this period including shortage of raw materials, critical components, lead time variability and production disturbances. After months of struggle enterprises are now moving from restoration towards regrowth. While many perceive the Connected Factory, Connected Supply Chain, and the Digital Manufacturing as few of the imperatives of Smart Manufacturing, the divergence between traditional process and advanced manufacturing methods is based on the possibilities of current improvements and technology adoption. The availability of data for timely orchestration and optimized execution is also an essential part of the manufacturing shift across the enterprise value chain.
Right now our focus is on addressing few of the existing gaps coupled with the widespread effect of the pandemic across supply chain, production process. The gradual adoption of a strategic model and the preparedness of the manufacturing sector towards smarter adoption, would eventually expedite the smart manufacturing process with an approach each manufacturer would require in resolving the immediate challenges the industry is facing. We have previously presented some smart factory case studies here.
The Black box – Rising to the challenge
Change is buffeting the industrial manufacturing industry comprising of the most innovative solutions and initiatives. However, there is no strategy to deploy the right solutions. For the manufacturer, the primary concern is building a cost-effective capacity, optimal product manufacturing and delivery, flexibility in product customization. The point we want to get across is that there is an implicit consideration of underlying issues across the chain which has been intensified by the pandemic. For example, the out-of-line supply chain is a major fallback during this time. Near-sourcing would be one of the significant moves as manufacturers would attempt to reduce or eliminate sole dependency on imports. Also, the supply network needs to be ideally optimized for minimum lead times. Consequently, the manufacturing ecosystem would be under continuous stress tests. The shift away from basic manufacturing towards digital technology based smart manufacturing will encourage organizations to reconsider how they operate. Hence, companies are building the capabilities to design and integrate systems, also managing the networks of suppliers to respond faster to the demand centricity and focus on the innovation areas.
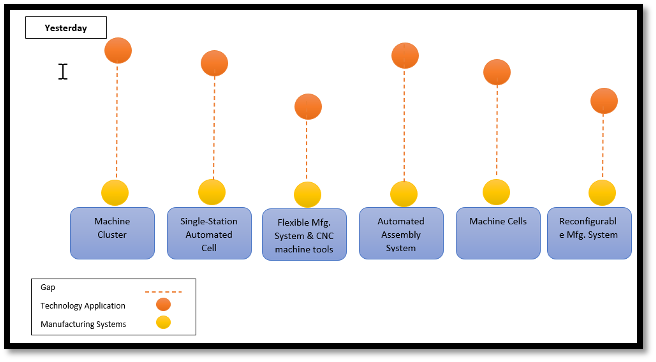
Fig 1. Technology adoption at an elemental level of manufacturing system
Fig 1. represents the gap between the manufacturing systems and technology implementation. A manufacturing system is usually a collection of integrated equipment, material handling technologies, including the manpower that drive the processing or assembly operations on a raw material. Though a manufacturing system may include more expansive concepts, this chart reflects the generic characteristics. Among the various manufacturing systems ‘Reconfigurable Manufacturing’ is closest to the technology application followed by Flexible Manufacturing Systems. Thus, implementation of smart solutions across most of the parts is unyielding and hard to achieve.
Manufacturing process is now matching up to the intelligent concepts and the right technology adoption. There are large number of innovative solutions and technologies developed to create a smart manufacturing system nevertheless, a digitalization roadmap is what will convert a conventional system into smart manufacturing system.
Progress towards a strategic model
To implement new or improved techniques and methods for smart manufacturing system, enterprises must develop internal capabilities and address high-impact challenges. Smart manufacturing is premised on different emerging and enabling technologies, but a plethora of companies struggle with the actual implications. So, when these enterprises formulate the smart manufacturing vision, they may be thrown off balance and think, “We have been automating and integrating manufacturing and business process for years, what is the difference?” Though these may seem up in the air discussions, capturing these five strategic imperatives may help the manufacturers in understanding the ramification of building a smart process.
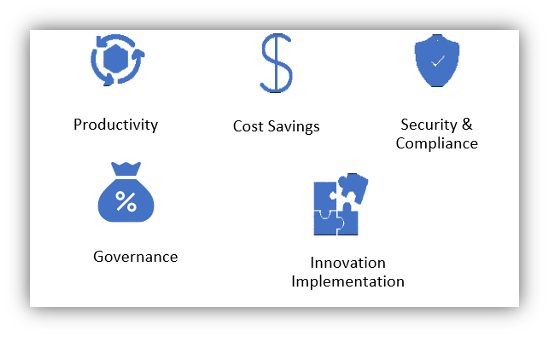
Fig 2. Parameters to build a strategic model
Crisis is an accelerator for digitalizing the processes. Manufacturers should heed the call to increase rate of production, address bottlenecks, reduced downtime, and human errors in addition to cost savings. Though machines are not infallible digital initiatives and automation do create a safer environment and drive productivity. However, to build trust in intelligent solutions, governance is essential. It can help maintain a balance for increased machine dependency, monitor performance, mitigate issues, and encourages enterprises to adopt newer ways of working. Nonetheless, machines can only replicate high-levels and partial cognition and cannot excel in creative thinking like humans. This is where the workforce is encouraged in developing skills and innovation.
Crisis fostering the transition
The manufacturer’s success swivels on multiple factors like select transformative technology, capability to identify business needs and desired outcomes, implement the technology or solution mapped to the anticipated value. With emerging competition, internal production and operation constraints coupled with COVID-19 pandemic are compelling the manufacturers to re-evaluate the manufacturing approach.
Smart manufacturing is gaining relevance and enterprises are re-strategizing the roadmap to build around capabilities. The groundwork should start with a contingency plan to address the end-to-end supply chain visibility, have access to the right data to support decision making and scaling deployments. In addition to these the pre-existing manufacturing problems are also influencing the shift from legacy practices to process modernization by adopting agile business models driving out redundancies and automating best practices.
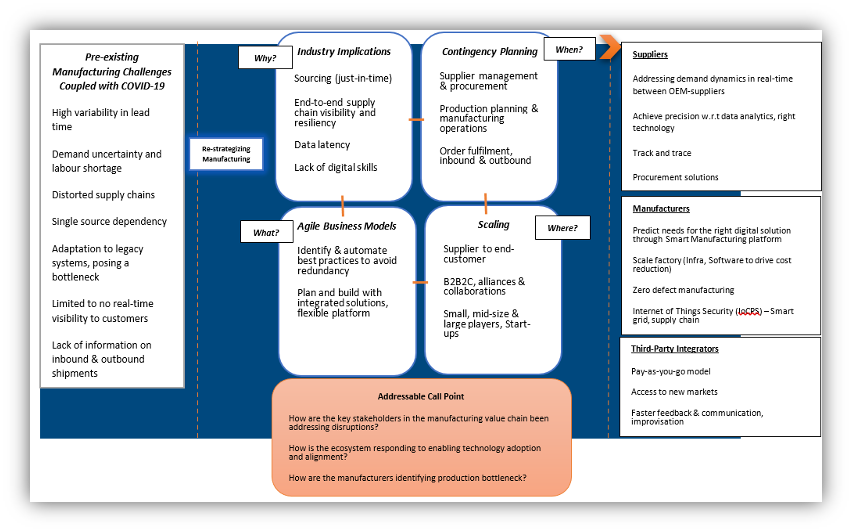
Fig 3. Transforming the manufacturing value chain through the 4Ws of smart adoption
Highlighting the impact of the volatility of the manufacturing process, the focus now shifts to the preparedness of the sector to fight a global crisis. According to Figure 4. re-strategizing the manufacturing process includes multitude of sources and managing all of them requires different approaches. The figure proposes a manufacturing transformation framework that outlines the core management clusters defined by industry concerns. The crux of the framework encompasses various obstacles that the manufacturers are facing and the extent to which the crisis has forced the sector to question the established traditional practices. At the same time the organizations have taken months to recover from process disruptions and see the need for a Contingency Plan to anticipate and respond to future interruptions. Addressing the severity of distorted supply chain, demand uncertainty, higher than expected lead-time variation would help in building a crisis resilient strategy, laying the groundwork for future-proofing manufacturing value chain. This will also prompt manufacturers to reduce single-source dependency and just-in-time process, agile enough to support new business models and solutions. With the collapse of conventional channels, organizations have been forced to adapt to new initiatives due demand uncertainties. When the consumer demand witnessed a steep decline in the automotive industry, there was a simultaneous spike in demand in the pharma and healthcare industry which influenced companies to diversify their businesses, respond and recover rapidly.
Additionally, agility is defined by scaling production, reconfiguring the supply network and moving to new avenues (e.g., brick and mortar to an ecommerce model). The implementation and scaling of digital and smart solutions is changing at an increasing pace. However, the power of collaborations will be an integral part of agility and adoption of smart manufacturing process. The need to strengthen the value-chain partnerships is crucial at the crossroads, this can only be enabled through real-time communication and improvisation.
However, while deploying intelligent manufacturing solutions few of the caveats include:
- High cost of implementation
- Lack of understanding on the cause of resistance and matter of choosing the right technology
- Hesitant to move “random adoption of technology” to “fit-to-purpose”
- Structural changes, capabilities, and the digital skills gap to drive transformation
- IT/OT convergence
- Services/products that stagnate at the pilot phase demonstrating unclear business value
- Every enterprise wants to stand-out, however the specific problem remains unsolved.
About the Author
This article was written by Titli Chatterjee. Titli has moved into a new role and organization from NASSCOM and has joined ISG (Information Services Group – https://isg-one.com/) in Research and Smart Manufacturing Practice. She has been leading ER&D/Industry 4.0 research initiatives of NASSCOM, having experience in research and consulting in the areas of emerging technologies and engineering services. She is closely working with the industry leaders, start-ups, government and other stakeholders in formulating a roadmap in disruptive technologies for Indian IT-BPM industry and highlighting how technology can be a game changer at the industrial front.